Products
Real Time Test Controller - RTC 9000
Real Time Test Controllers
RTC 9000
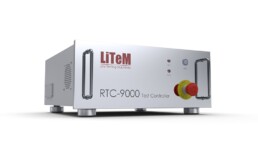
The RTC 9000 controller range has been developed and assembled in Italy, using the best available technologies; essential to perform precise and reliable mechanical structural tests, allowing for the management of different types of actuators and motors.
The RTC 9000 is a multi-axial controller (expandable up to 4 active axes); it can run static and cyclical tests both in displacement control, force control, aux (+/-10V) channel control and Encoder control; controlling simultaneously all the active axes. Additional 4 read-only analog input channels (synchronous with the active axes) complete the potential of this controller.
The RTC 9000 is the great controller for more complex tests that require the use of multiple simultaneous axes on the same object under test.
The system is configured in pneumatic mode (P) for the management of pneumatic actuators, electric mode (E) for the management of electric actuators or hydraulic mode (H) for the management of hydraulic actuators.
Applications
- STATIC YIELD/FAILURE TESTING on composite materials and dental implants, etc.;
- STIFFNESS TESTING on single and assembled components, metal, plastic and composite material products, 3D-printed and biological material products;
- DYNAMIC TESTING with sine, pulsed square wave with settable duty cycle or constant speed triangle wave (e.g. for characterisation of suspensions/shock absorbers);
- CONSTANT AMPLITUDE FATIGUE TESTING to determine the life under cyclic/repeated loads for any type of component (Wöhler curves);
- CONSTANT AMPLITUDE BLOCK FATIGUE TESTING for the determination of the Palmgren-Miner relation and of the actual damage value;
- VARIABLE AMPLITUDE FATIGUE TESTING using the reproduction/simulation in the laboratory of real world load curves acquired on-site;
- REPRODUCTION OF LOAD CURVES Defined by the user during design phase, simulation of seismic tests.
Real Time Test Controller - RTC 9002
Real Time Test Controllers
RTC 9002
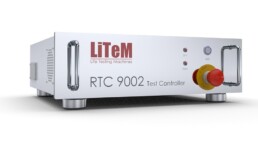
The RTC 9002 controller range has been developed and assembled in Italy, using the best available technologies; essential to perform precise and reliable mechanical structural tests, allowing for the management of different types of actuators and motors.
The RTC 9002 is a bi-axial controller (non-expandable); it can run static and cyclical tests both in displacement control, force control, aux (+/-10V) channel control and Encoder control; controlling simultaneously the two active axes. Additional 4 read-only analog input channels (synchronous with the active axes) complete the potential of this controller.
The RTC 9002 is the great controller for bikes and bicycle tests (as per ISO 4210); pedalling tests, handlebar tests, bike frame stiffness tests and all those applications in which bi-axial tests have to be done.
The system is configured in pneumatic mode (P) for the management of pneumatic actuators, electric mode (E) for the management of electric actuators or hydraulic mode (H) for the management of hydraulic actuators.
Applications
- STATIC YIELD/FAILURE TESTING on composite materials and dental implants, etc.;
- STIFFNESS TESTING on single and assembled components, metal, plastic and composite material products, 3D-printed and biological material products;
- DYNAMIC TESTING with sine, pulsed square wave with settable duty cycle or constant speed triangle wave (e.g. for characterisation of suspensions/shock absorbers);
- CONSTANT AMPLITUDE FATIGUE TESTING to determine the life under cyclic/repeated loads for any type of component (Wöhler curves);
- CONSTANT AMPLITUDE BLOCK FATIGUE TESTING for the determination of the Palmgren-Miner relation and of the actual damage value;
- VARIABLE AMPLITUDE FATIGUE TESTING using the reproduction/simulation in the laboratory of real world load curves acquired on-site;
- REPRODUCTION OF LOAD CURVES Defined by the user during design phase, simulation of seismic tests.
Real Time Test Controller - RTC 9001
Real Time Test Controllers
RTC 9001
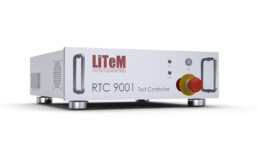
The RTC 9001 controller range has been developed and assembled in Italy, using the best available technologies; essential to perform precise and reliable mechanical structural tests, allowing for the management of different types of actuators and motors.
The RTC 9001 is a mono-axial controller (non-expandable); it can run static and cyclical tests both in displacement control, force control, aux (+/-10V) channel control and Encoder control. Additional 4 read-only analog input channels (synchronous with the active axis) complete the potential of this controller.
The system is configured in pneumatic mode (P) for the management of pneumatic actuators, electric mode (E) for the management of electric actuators or hydraulic mode (H) for the management of hydraulic actuators.
Applications
- STATIC YIELD/FAILURE TESTING on composite materials and dental implants, etc.;
- STIFFNESS TESTING on single and assembled components, metal, plastic and composite material products, 3D-printed and biological material products;
- DYNAMIC TESTING with sine, pulsed square wave with settable duty cycle or constant speed triangle wave (e.g. for characterisation of suspensions/shock absorbers);
- CONSTANT AMPLITUDE FATIGUE TESTING to determine the life under cyclic/repeated loads for any type of component (Wöhler curves);
- CONSTANT AMPLITUDE BLOCK FATIGUE TESTING for the determination of the Palmgren-Miner relation and of the actual damage value;
- VARIABLE AMPLITUDE FATIGUE TESTING using the reproduction/simulation in the laboratory of real world load curves acquired on-site;
- REPRODUCTION OF LOAD CURVES Defined by the user during design phase, simulation of seismic tests.
Software Tool PROFILE EDITOR
Tool
Software Tool PROFILE EDITOR
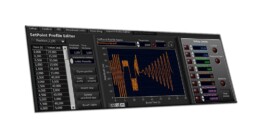
Profile Editor Tool is an additional component of the RTC 9000 software which allows variable profile, cyclical fatigue tests to be performed. The profile is generated directly by the operator on the software interface or with an external text editor and then loaded quickly onto the software tool.
The PROFILE EDITOR tool is essential when the replication is required for variable profile load curves, arising from acquisitions performed through sensors and data loggers applied directly on the component during normal operation or during in-field tests.
The test profile can equally be set with the control procedures available in RTC 9001 and RTC 9000 controller series, that is:
- Position control
- Force control
- AUX 1 control (auxiliary channel)
- Control with Encoder
The Time and Amplitude multiplier functions enable the designed profile to be changed quickly, by intervening on the times and amplitude of the measures selected for running the test (force-position- Aux1-encoder).
It is possible to select 4 different modes for interpolation of the points that define the profile.
The PROFILE EDITOR tool software is also applicable to RTC 9000 multi-axial systems. In this case it will be possible to assign a different load curve (profile) to each actuator. These profiles can be performed at the same time. PROFILE EDITOR is indispensable for pedalling test as per ISO 4210-6.
Utilities
Video Applications
Software and Tools
SOFTWARE AND TOOLS
The SS 9000 Software Suite is designed to run static, semi-static and fatigue tests both with single-axis and multi-axes systems.
The software is compatible with all RTC 9000 controllers and with all software tools developed by LiTem.
PROFILE EDITOR Tool is an additional component of the SS 9000 software suite which allows variable profile, cyclical fatigue tests to be performed. It is essential when the replication is required for variable profile load curves, arising from in-field acquisitions or from user defined ones.
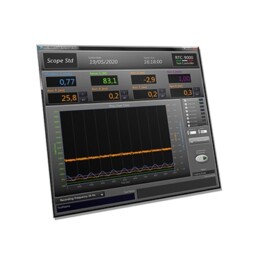
Software Tool SCOPE
The software tool SCOPE activates the reading mode of 4 analogue channels of the RTC 9000 and RTC 9001 controllers. The tool allows to display and record the acquired values by the additional channels in a synchronised way with the test values of channel 1 of the controller.
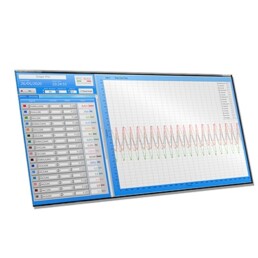
Software Tool SCOPE PRO
The software tool SCOPE PRO activates the reading mode of 4 analogue channels of the RTC 9000 and RTC 9001 controllers. The tool allows to display and record the acquired values by the additional channels in a synchronised way with the test values of all channels (up to 4 axes) of the controller. The operator can set the inputs to be displayed and recorded.
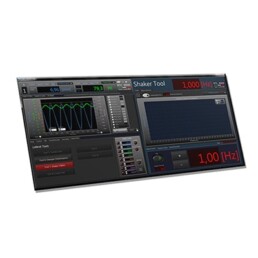
Software Tool SHAKER
The software tool SHAKER is used for tests on vibrating tables or shakers. Tests can be run with frequency set in manual or automatic mode and tests with frequency sweep with constant acceleration.
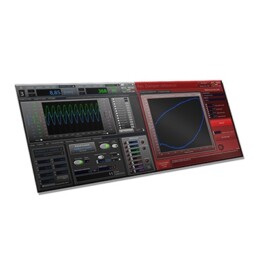
Software Tool DAMPER
The software tool DAMPER allows the operator to run tests on any kind of shock absorber. The operator can set reference curves and monitor the actual performance of the shock absorber. This is ideal for quality checks during production and in maintenance and assistance phases.
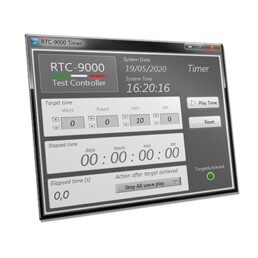
Software Tool TIME
The software tool TIME allow to set the duration of the fatigue test, using time definition instead of number of cycles. The test is interrupted when the set time has elapsed.
Eldy 10
Electrodynamic testing system
ELDY 10
The electrodynamic testing systems in the ELDY 10 family have been designed to run static, semi-static, dynamic and fatigue tests on a large variety of components and materials.
ELDY systems use motors with voice coil technology and single-phase power supply. Combined with RTC 9001 Controller and SS 9000 software, ELDY systems allow to reach high test frequency and displacement micrometric accuracy.
The presence of the movable cross strut and the width of the work surface make it easy to attach and grip even the most complex samples.
Utilities

oil free

low consumption

low noise

high flexibility

table top

simple to use
Application
The ELDY 10 testing machines allow various types of configurations to be achieved in terms of actuator strokes; the maximum force is 10 N. The simple and intuitive software interface makes the ELDY 10 systems perfect for the following sectors:
- Biomedical
- R&D
- Plastics
- Rubber
- 3D Printing (plastics e metals)
- Composit materials
- Electronic components and hardware
- Fabrics and tissues
- Biological matrerials
SS9000 Software Suite
Software
SS 9000 Software Suite
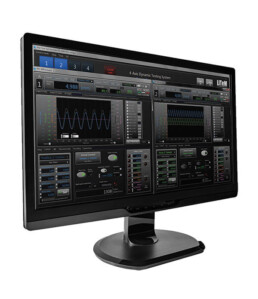
The SS 9000 software is designed to run static, semi-static and fatigue tests both with single-axis and multi-axes systems. Tests can be run either for:
- Position
- Force
- Encoder
- AUX Auxiliary Channel
For each axis and for any control procedure, the test can be set in ramp mode (for static and semi-static tests) or with sine, triangular or square wave.
The SS 9000 software suite allows interfacing to the RTC series controllers and allows the complete management of tests. It is possible to set the test parameters, the command and safety parameters, the real-time display of the command signals and the recording and saving modes of the acquired data. The video tutorials regarding the complete use of the software are provided and are available on LiTem’s YouTube channels.
Additional tools can be provided on request in order to implement SS 9000 software functions and to manage user customized tests. LiTem can design new software tools following the customer’s specifications.
The extreme ease of use and the intuitive interface make the SS 9000 software suite an indispensable and extremely reliable tool for carrying out all tests with LiTem systems.
Utilities
Video Applications
Prima PN
Pneumatic Testing System
Prima PN
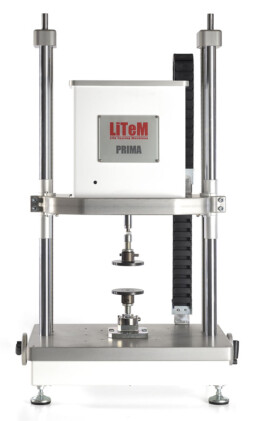
The PRIMA PN test machine, made with a pneumatic actuator, has been designed to run static, semi-static, dynamic and fatigue tests on a large variety of components and materials.
Combined with an RTC 9001 controller and related software, the PRIMA PN system is the ideal solution for use in a range of fields.
The presence of the movable cross strut and the width of the work surface make it easy to attach and grip even the most complex samples.
Reliability, accuracy, an eye-catching design and the “table top” configuration, make the PRIMA PN the perfect test machine for every test laboratory.
Utilities

oil free

low consumption

maximum flexibility

table top

easy to use
Applications
The PRIMA PN machine can be used in a wide range of applications thanks to the possibility of achieving a number of different configurations in terms of pneumatic actuator strokes.
The simple and intuitive software interface makes the products in the PRIMA PN series perfect for the following sectors:
- Biomedical
- R&D
- Plastics
- Rubber
- 3D Printing (plastics e metals)
- Composit materials
- Springs
- Mechanical components