Real Time Test Controllers
RTC 9000
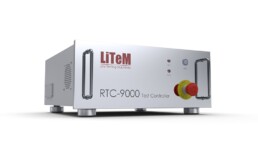
The RTC 9000 controller range has been developed and assembled in Italy, using the best available technologies; essential to perform precise and reliable mechanical structural tests, allowing for the management of different types of actuators and motors.
The RTC 9000 is a multi-axial controller (expandable up to 4 active axes); it can run static and cyclical tests both in displacement control, force control, aux (+/-10V) channel control and Encoder control; controlling simultaneously all the active axes. Additional 4 read-only analog input channels (synchronous with the active axes) complete the potential of this controller.
The RTC 9000 is the great controller for more complex tests that require the use of multiple simultaneous axes on the same object under test.
The system is configured in pneumatic mode (P) for the management of pneumatic actuators, electric mode (E) for the management of electric actuators or hydraulic mode (H) for the management of hydraulic actuators.
Applications
- STATIC YIELD/FAILURE TESTING on composite materials and dental implants, etc.;
- STIFFNESS TESTING on single and assembled components, metal, plastic and composite material products, 3D-printed and biological material products;
- DYNAMIC TESTING with sine, pulsed square wave with settable duty cycle or constant speed triangle wave (e.g. for characterisation of suspensions/shock absorbers);
- CONSTANT AMPLITUDE FATIGUE TESTING to determine the life under cyclic/repeated loads for any type of component (Wöhler curves);
- CONSTANT AMPLITUDE BLOCK FATIGUE TESTING for the determination of the Palmgren-Miner relation and of the actual damage value;
- VARIABLE AMPLITUDE FATIGUE TESTING using the reproduction/simulation in the laboratory of real world load curves acquired on-site;
- REPRODUCTION OF LOAD CURVES Defined by the user during design phase, simulation of seismic tests.